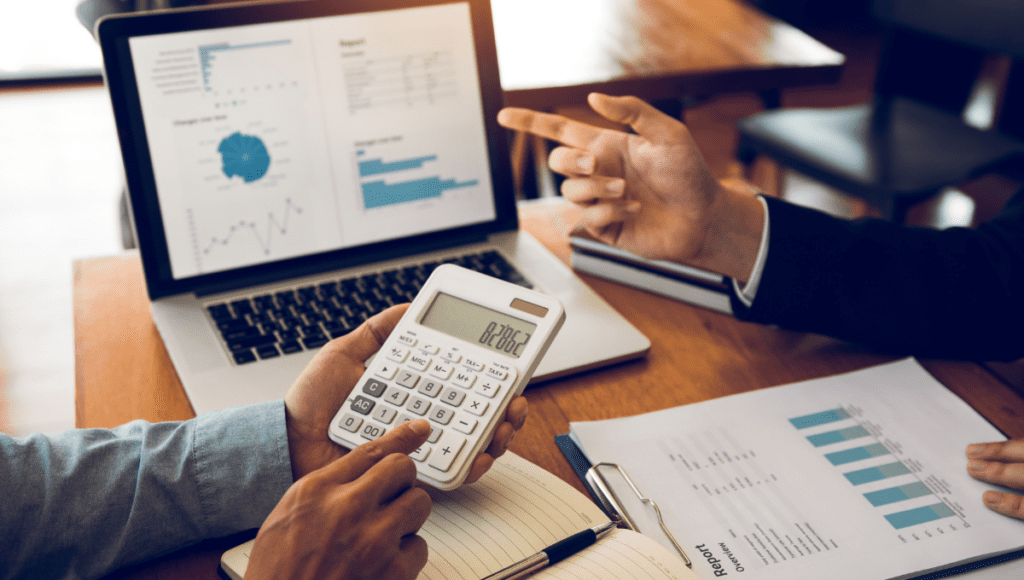
In the dynamic world of engineering project management, cost improvement is not merely a necessity but the lifeblood of sustainable success. This article offers a review of some multifaceted approaches of various cost improvement strategies, from immediate actions to long-term frameworks. It examines cost-improvement applications through a project management lens.
Cost Improvement – The Lifeblood of Success
Projects have cost constraints. How much is the company investing in this project? This investment is compared against the income generated, or Return on Investment, ROI. Additionally, if our project produces a product, the associated material and manufacturing costs will impact the product’s pricing and sales.
Understanding the various avenues for cost reduction is the foundation of any successful cost improvement strategy. A hyperfocus on a single approach will exclude the myriad possibilities of varying levels of sophistication. Once the product is created, it can be challenging to justify tooling changes or major manufacturing line updates.
Short, Medium, and Long-Term Approaches
Effective cost management requires a refined approach that balances immediate needs with future goals. Short-term strategies might include quick wins like renegotiating supplier contracts or optimizing inventory levels. Most project scopes fall into this category, especially for new projects.
Medium-term strategies often involve more substantial changes, such as process reengineering or adopting new technologies. From experience, the project can be undertaken to consolidate manufacturing lines or products generated from multiple manufacturing lines.
Long-term approaches focus on foundational shifts, like investing in R&D for cost-efficient materials or developing new business models. As an engineering manager, your role in navigating these timelines and aligning your strategies with organizational goals is crucial. Your commitment ensures sustained cost improvement.
Product and Business Approaches
A holistic approach to cost improvement encompasses both product-specific and business-wide strategies. Techniques such as Value Propositions and Value Stream Mapping are critical for identifying and eliminating waste within product development and business processes. Methods like the Function Allocation System Technique (FAST) and Design to Value (DTV) help managers optimize product design for cost efficiency without compromising quality. Moreover, adopting Design for Manufacturing and Assembly principles can significantly streamline production and reduce costs.
Manufacturing Cost Improvement
Manufacturing efficiency is a cornerstone of cost reduction. Techniques like 5S (Sort, Set-in-Order, Shine, Standardize, and Sustain) and Lean manufacturing are essential for engineering managers aiming to create more efficient, less wasteful production environments. Real-world case studies provide practical insights into how these methodologies can be successfully implemented, highlighting the importance of continuous improvement and employee involvement in the cost-improvement journey.
Material substitutions can also be significant sources of cost improvement. From experience, a project team that does not commit too soon to a single design proposal can optimize the product cost from the beginning of the product lifecycle.
Platform Management
Platform management is a strategic approach that can lead to significant cost savings by promoting component standardization and modular design. By focusing on common platforms, organizations can streamline their development processes, reduce redundancy, and achieve economies of scale. This approach involves creating a shared infrastructure or framework that supports multiple products or services, which helps in minimizing the variety of components needed and simplifying maintenance. Standardization reduces the complexity of managing different parts, while modular design allows for flexibility and adaptability in response to changing requirements or technological advancements. By reusing established platforms, companies can accelerate time-to-market, improve consistency, and lower the overall costs associated with product development and lifecycle management.
Cost Improvement through Quality
Quality and cost improvement are inherently linked, as higher quality standards directly contribute to reduced operational costs by minimizing defects and the need for costly rework. Techniques for quality improvement, such as Verification and Design for Six Sigma (DFSS), are instrumental in addressing potential issues before they manifest into problems. Verification ensures that all design and production processes meet the specified requirements and standards, thereby identifying and rectifying discrepancies early in the development cycle. Design for Six Sigma (DFSS) takes this a step further by integrating quality improvement principles into the design phase, aiming to create products that meet or exceed customer expectations with minimal variation. By focusing on quality from the outset, organizations can avoid the substantial costs associated with post-production fixes and rework, leading to more efficient operations and higher profitability.
Total Quality Management
Ideally, we have created or encouraged a continuous improvement effort that starts with our projects, ensuring that quality and efficiency are embedded into every phase of development. This approach is crucial for fostering a culture of ongoing enhancement and adapting to evolving challenges. Our preferred methodology for driving continuous improvement is Total Quality Management (TQM). TQM stands out as our favorite approach due to its comprehensive and inclusive nature. The tools and techniques associated with TQM are straightforward, making them accessible to team members at all levels. This ease of use helps ensure that quality management practices are consistently applied across projects, from inception to delivery.
Customer Focus:
The primary focus of TQM is to meet and exceed customer expectations. Every employee, from top management to the frontline workers, should understand the customer’s needs and strive to deliver products and services that fulfill those needs.
Continuous Improvement:
TQM is an ongoing process of identifying, reducing, and eliminating suboptimal processes in manufacturing, service delivery, and other organizational functions. Continuous improvement seeks to enhance the processes and systems incrementally.
Employee Involvement:
All employees are encouraged to participate in the quality improvement process. Employee involvement includes training, empowerment, and collaboration to contribute ideas and solutions for quality enhancement.
Process-Centered Approach:
TQM focuses on optimizing and managing the processes involved in production and service delivery. Understanding and controlling the process ensures that the output meets quality standards.
Integrated System:
Quality management should be integrated into the organization’s overall management system. This integration ensures that quality principles are part of the organizational culture and decision-making processes.
Strategic and Systematic Approach:
A strategic plan that includes quality as a core component is essential for long-term success. TQM requires a systematic approach to integrating quality management into every organization facet.
Decision-Making Based on Facts:
TQM emphasizes data-driven decision-making. Accurate data collection and analysis are crucial for identifying problems, understanding root causes, and evaluating the effectiveness of quality improvements.
Communication:
Effective communication is vital for the successful implementation of TQM. Open and transparent communication channels ensure that everyone in the organization is aware of quality goals, processes, and outcomes.
Customer-Supplier Partnerships:
Developing strong relationships with both internal and external customers and suppliers is crucial. These partnerships help us better understand requirements and ensure that quality standards are met at every stage of the supply chain.
Leadership:
Leadership is pivotal in establishing a vision and direction for quality management. Leaders should inspire, guide, and support their teams in achieving quality objectives.
Benchmarking:
Comparing the organization’s processes and performance metrics with industry best practices helps identify areas for improvement. Benchmarking is a tool for learning and implementing superior practices.
Training and Education:
Continuous training and education for employees at all levels ensure they have the necessary skills and knowledge to improve quality.
Zero Defects:
A fundamental principle of TQM is striving for zero defects by identifying and eliminating sources of errors. This goal drives organizations to achieve higher quality standards consistently.
Innovative Approaches to Cost Improvement
Innovation is crucial for maintaining a competitive edge in the engineering field, as it drives progress, enhances capabilities, and differentiates organizations from their competitors. To foster innovation, various ideas-generating techniques can be employed, each offering unique benefits. For instance, brainstorming encourages the free exchange of ideas among team members, allowing for creative solutions and novel approaches to problem-solving. Organization development methods focus on improving organizational effectiveness and fostering a culture that supports innovation. This might include structuring teams for greater collaboration or implementing practices that encourage continuous learning and improvement.
In addition to these traditional methods, the integration of Artificial Intelligence (AI) into cost improvement strategies represents a significant advancement in the field. AI technologies, such as machine learning and data analytics, offer new insights and efficiencies by analyzing vast amounts of data to identify patterns, predict outcomes, and optimize processes. AI can streamline operations, enhance decision-making, and uncover cost-saving opportunities that may not be immediately apparent through conventional methods. For example, AI-driven predictive maintenance can foresee equipment failures before they occur, reducing downtime and repair costs. By leveraging AI, organizations can achieve greater precision in their cost management strategies and drive innovation in their engineering practices, ultimately leading to more effective and competitive outcomes.
Conclusion
We have many approaches to improving product costs, from material selection to delivery. Creating a project environment conducive to team engagement and balancing speed with exploration and learning improves the possibility of finding a cost-effective solution. This will save us greatly over the product lifecycle.
Related Content
Transformation Corner: The Intersection of Product and Project Managers
Integrating Change Orders in Microsoft Project: A Step-by-Step Guide
From Opportunity to Project Scope: Bridging the Gap for Successful Project Delivery
Elevate your project management skills and propel your career forward with an MPUG Membership. Gain access to 500+ hours of PMI-accredited training, live events, and a vibrant online community. Watch a free lesson and see how MPUG can teach you to Master Projects for Unlimited Growth. JOIN NOW