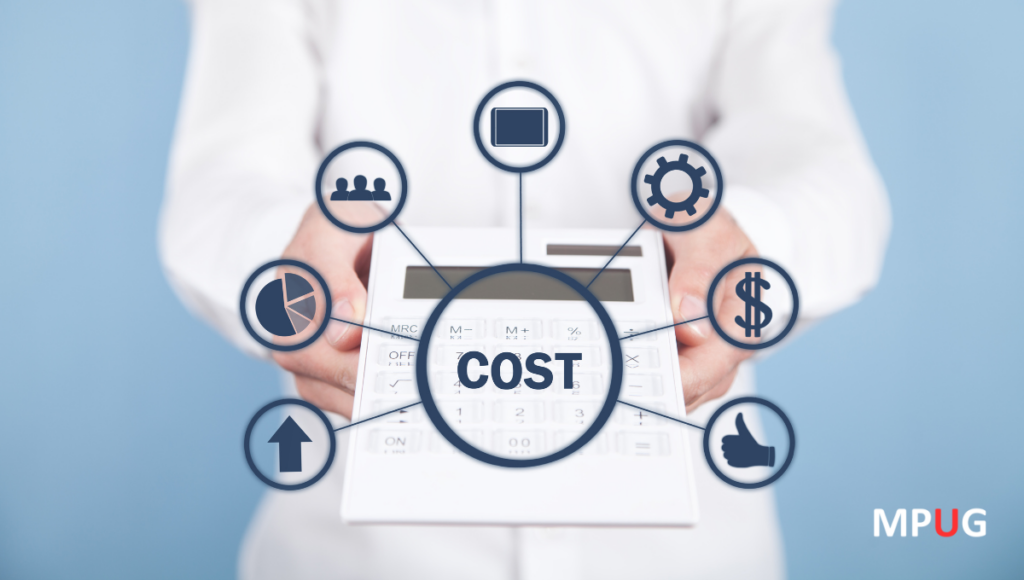
Product development and managing engineering projects comes with considerable uncertainty regarding cost. Improvement is not merely a necessity but the lifeblood of sustainable success. Fortunately, we have a range of approaches that support our cost improvement strategies, from immediate actions to long-term frameworks. Essentially, we want to maximize the value, which requires delivering a benefit greater than the costs.

Improvement – The Lifeblood of Success
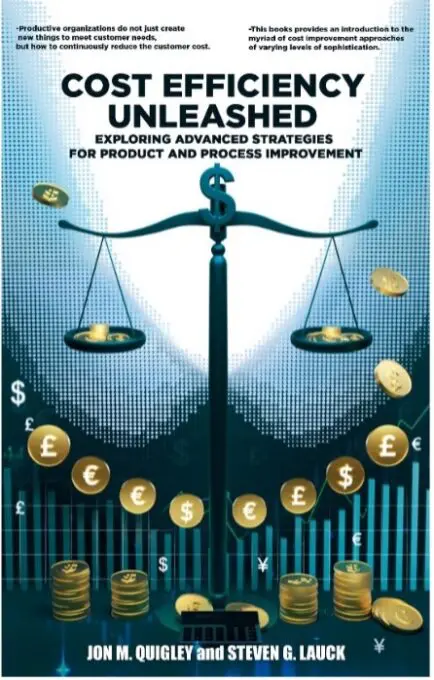
Projects have cost constraints.
How much is the company investing in this project? This investment is compared against the income generated, or Return on Investment (ROI).
Additionally, if our project produces a product, the associated material and manufacturing costs will impact the product’s pricing and subsequent sales.
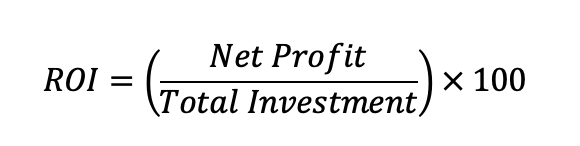
Understanding the various avenues for cost reduction is the foundation of any successful cost improvement strategy. A hyperfocus on a single approach will exclude the myriad possibilities of varying levels of sophistication. Once the product is created, it can be challenging to justify costly tooling changes or major manufacturing line updates. In this regard, unless well planned, incremental approaches are not probable.
Short, Medium, and Long-Term Approaches
Effective cost management requires a refined approach that balances immediate needs with future goals. Short-term strategies might include quick wins like renegotiating supplier contracts or optimizing inventory levels. Most project scopes fall into this category, especially for new projects. This of course is linked to the expected duration of the project or the delivery date of the results.
Medium-term strategies often involve more substantial changes, such as process reengineering or adopting new technologies. From experience, the project can be undertaken to consolidate manufacturing lines or products generated from multiple manufacturing lines.
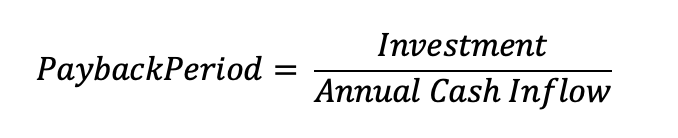
Long-term approaches focus on foundational shifts, like investing in R&D-backed projects, applying new materials, using relatively unfamiliar technology, or developing new business models. As an engineering project manager, your role in navigating these timelines and aligning your strategies with organizational goals is crucial. Product development often comes with considerable uncertainty. You and the team will learn along the way and be able to react to these emerging learnings effectively. The commitment of the project manager and the team ensures sustained cost improvement.
Product and Business Approaches
A holistic approach to cost improvement encompasses both product-specific and business-wide strategies. Techniques such as Value Propositions and Value Stream Mapping are critical for identifying and eliminating waste within product development and business processes. Methods like the Function Allocation System Technique (FAST) and Design to Value (DTV) help optimize product design for cost efficiency without compromising quality. During the manufacturing line development, Design for Manufacturing and Assembly (DFMA) principles can significantly streamline production and reduce costs.
Manufacturing Cost Improvement
Manufacturing efficiency is a cornerstone of cost reduction. Techniques like 5S (Sort, Set-in-Order, Shine, Standardize, and Sustain) and Lean manufacturing are essential for engineering managers aiming to create more efficient, less wasteful production environments. Real-world case studies provide practical insights into how these methodologies can be successfully implemented, highlighting the importance of continuous improvement and employee involvement in the cost-improvement journey.
Material substitutions can also be significant sources of cost improvement. From experience, a project team that does not commit too soon to a single design proposal can optimize the product cost from the beginning of the product lifecycle. We recommend the book “The Lean Machine” by Dantar P. Oosterwal.[1]
Platform Management
Platform management is a strategic approach that can lead to significant cost savings by promoting component standardization and modular design. Organizations can streamline their development processes, reduce redundancy, and achieve economies of scale by focusing on common platforms or elements. This approach involves creating shared components or portions of the product, infrastructure, or framework that support multiple products or services, which helps in minimizing the variety of components needed and simplifying maintenance. Standardization reduces the complexity of managing different parts, while modular design allows flexibility and adaptability in response to changing requirements or technological advancements. By reusing established platforms, companies can accelerate time-to-market, improve consistency, and lower the overall costs associated with product development and lifecycle management.
Material Substitution
Material substitution can help us achieve our cost goals. Replacing one material with another with similar or suitable properties but at a lower cost aims to reduce the direct material costs associated with the product while maintaining its functionality and quality. Design optimization involves analyzing the results of learning continuously and refining the product design iteratively, identifying opportunities for cost reduction without compromising performance or quality. This approach focuses on streamlining features, reducing complexity, and eliminating unnecessary components or processes.
Function Allocation System Technique (FAST)
Function allocation is a systematic technique used in systems engineering to allocate and assign functions to specific components or elements within a system. Function allocation ensures that each part is appropriately assigned to the most suitable aspect, considering performance, efficiency, reliability, and human factors. This technique helps optimize the system’s overall design and implementation by aligning functions with the capabilities and characteristics of the system elements.
Design to Value
The Design to Value (DtV) approach significantly enhances business operations by streamlining product development and manufacturing processes. By focusing on the most valuable features from a customer’s perspective, businesses can allocate resources more efficiently, reducing waste and lowering production costs. This strategic prioritization enables companies to optimize their supply chain and inventory management as they manufacture products that align closely with market demand. Furthermore, DtV facilitates quicker decision-making and reduces time to market, enhancing the company’s responsiveness to market changes and customer needs.
Cost Improvement through Quality
Quality and cost improvement are inherently linked, as higher quality standards directly contribute to reduced operational costs by minimizing defects and the need for costly rework. This is so important that there will be times when a project is undertaken with the explicit scope to reduce the quality costs of a product or service. Whether this is an effort to produce a new product or improve the specific costs of an existing product, the project and the team can make use of these techniques to deliver the results we desire.
Techniques for quality improvement, such as Verification and Design for Six Sigma (DFSS), are instrumental in addressing potential issues before they manifest into problems. Verification ensures that all design and production processes meet the specified requirements and standards. In the automotive world, we have activities such as design for manufacturing and assembly (DFMA), we also test process results as we develop the manufacturing line through process failure mode effects analysis and control plan development. These steps help identify and rectify discrepancies early in the development cycle. Design for Six Sigma (DFSS) takes this further by integrating quality improvement principles into the design phase, aiming to create products that meet or exceed customer expectations with minimal variation. By focusing on quality from the outset, organizations can avoid the substantial costs associated with post-production fixes and rework, leading to more efficient operations and higher profitability.
Total Quality Management
Ideally, we have created or encouraged a continuous improvement effort that starts with our projects, ensuring that quality and efficiency are embedded into every development phase. This approach is crucial for fostering a culture of ongoing enhancement and adapting to evolving challenges. Our preferred methodology for driving continuous improvement is Total Quality Management (TQM). TQM is our favorite approach due to its comprehensive and inclusive nature. The tools and techniques associated with TQM are straightforward, making them accessible to team members at all levels. This ease of use helps ensure that quality management practices are consistently applied across projects, from inception to delivery. Personally, I like this approach as the tools and techniques espoused are egalitarian and easy to use. One does not need to be a quality professional or an engineer to use these tools and produce significant results.
Basic Quality Tools
- Cause-and-Effect Diagram (Ishikawa or Fishbone Diagram)
- Helps identify root causes of a problem.
- Check Sheet
- A structured form for collecting and analyzing data.
- Control Chart
- Monitors process variation over time.
- Histogram
- Shows the frequency distribution of data.
- Pareto Chart
- Highlights the most important factors using the 80/20 rule.
- Scatter Diagram
- Displays relationships between two variables.
- Flowchart (Process Diagram)
- Visualizes the steps in a process.
Additional TQM Tools
- Affinity Diagram
- Organizes ideas into natural groupings.
- Failure Modes and Effects Analysis (FMEA)
- Identifies potential failure points in a process.
- Force Field Analysis
- Analyzes forces for and against a change.
- Benchmarking
- Compares processes against best-in-class standards, processes, and products.
- PDCA Cycle (Plan-Do-Check-Act)
- A cyclical model for continuous improvement.
- Root Cause Analysis (RCA)
- A method for identifying the source of problems.
- 5 Whys
- A technique to drill down to the root cause by repeatedly asking “why.”
Value Engineering
Value engineering is a systematic and structured approach that focuses on maximizing the value of a product, process, or system by optimizing its cost, quality, and performance. It involves analyzing various components, functions, and requirements to identify opportunities for cost reduction, improved efficiency, increased functionality, and enhanced overall value. The primary goal of value engineering is to achieve the desired performance and functionality at the lowest possible cost without compromising quality or customer satisfaction.
Value Analysis
Value analysis, sometimes used interchangeably with value engineering, focuses specifically on analyzing and evaluating the value provided by a product or system. It systematically examines the functions and costs of each component or feature to determine its valuable contribution. Value analysis aims to identify opportunities to enhance value by eliminating unnecessary costs, improving functionality, or reducing complexity. There are some critical steps in value analysis.
Value Stream Mapping
Value Stream Mapping (VSM) is a lean management technique used to analyze, visualize, and improve the flow of materials, information, and activities required to deliver a product or service to the customer. It provides a comprehensive view of the entire value stream, highlighting areas of waste and opportunities for improvement.

Training and Education
Continuous training and training for employees at all levels ensure they have the necessary skills and knowledge to improve quality. Our organization is powered by the people who do the work, our projects are successful when the talent and motivation rises to meet the challenges as these become known.
It is to the benefit of organization and the PMO at large to have a well skilled talent base. Developing a constant learning organization is key to continuous improvement. This learning provides our team members with tools and techniques to respond to the things that arise by experimenting with those tools in the project’s service.
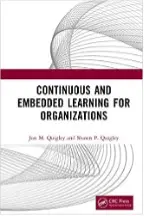
Innovative Approaches to Cost Improvement
Innovation is crucial for maintaining a competitive edge in the engineering field, as it drives progress, enhances capabilities, and differentiates organizations from their competitors. Various ideas-generating techniques can be employed to foster innovation, each offering unique benefits. For instance, brainstorming encourages the free exchange of ideas among team members, allowing for creative solutions and novel approaches to problem-solving. Organization development methods focus on improving organizational effectiveness and fostering a culture that supports innovation. This might include structuring teams for greater collaboration or implementing practices that encourage continuous learning and improvement.
Brainstorming
Brainstorming is a powerful technique that harnesses a team’s collective creativity and knowledge to generate innovative ideas and solutions. When applied to cost-improvement initiatives, brainstorming can uncover valuable insights and strategies to reduce expenses and enhance financial performance. We have used this technique to generate many potential ideas, from which we can prioritize and select later.
De Bono’s Six Thinking Hats
Dr. Edward de Bono’s Six Thinking Hats is a robust group discussion and individual thinking tool that helps streamline brainstorming sessions, decision-making processes, and problem-solving. The benefit of De Bono’s Six Thinking Hats is perspective. Each hat pushes us to think from a different perspective. The variety of perspectives gives us a better idea of what might be valid. This method is particularly effective in cost-reduction brainstorming because it ensures a multifaceted examination of the issue, allowing participants to explore all aspects before deciding.
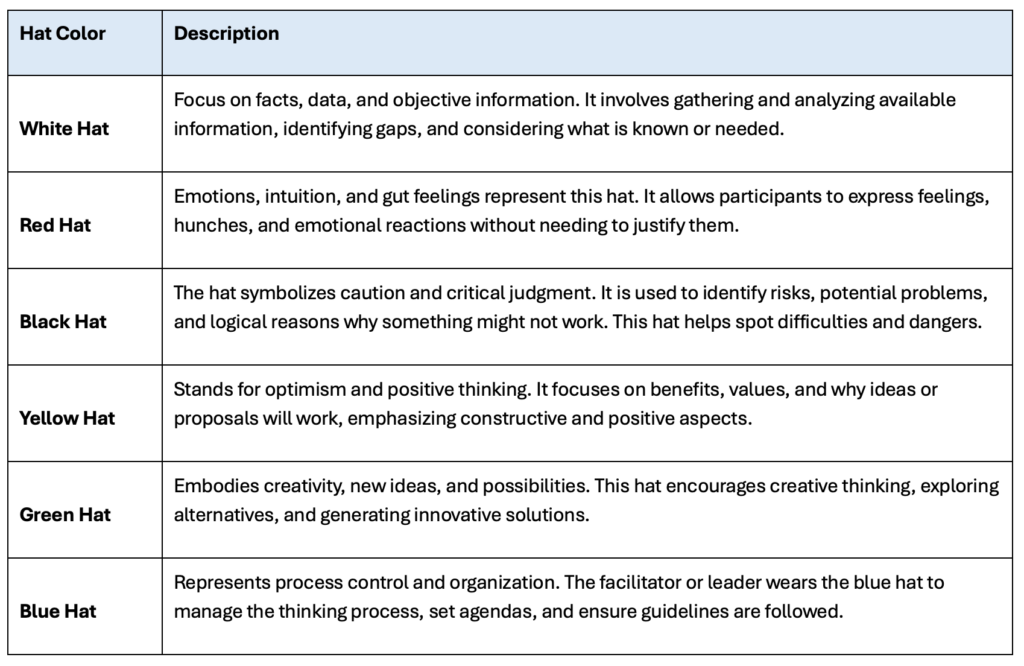
Artificial Intelligence
In addition to these traditional methods, the integration of Artificial Intelligence (AI) into cost improvement strategies represents a significant advancement in the field. AI technologies, such as machine learning and data analytics, offer new insights and efficiencies by analyzing vast amounts of data to identify patterns, predict outcomes, and optimize processes. AI can streamline operations, enhance decision-making, and uncover cost-saving opportunities that may not be immediately apparent through conventional methods. For example, AI-driven predictive maintenance can foresee equipment failures before they occur, reducing downtime and repair costs. By leveraging AI, organizations can achieve greater precision in their cost management strategies and drive innovation in their engineering practices, ultimately leading to more effective and competitive outcomes.
Conclusion
We have many approaches to improving our project and product costs, from material selection to delivery. Creating a project environment conducive to team engagement and balancing speed with exploration and learning improves the possibility of finding a cost-effective solution, which will save us greatly over the product lifecycle.
References
[1] https://www.amazon.com/s?k=the+lean+machine&crid=KZWIPOD5JG2I&sprefix=the+lean+machin%2Caps%2C127&ref=nb_sb_noss_2
[1] K. Pries and J. M. Quigley, “Reducing Process Costs with Lean, Six Sigma, and Value Engineering Techniques,” CRC Press, Boca Raton, 2013.
[2] D. P. Oosterwal, The Lean Machine: How Harley-Davidson Drove Top-Line Growth and Profitability with Revolutionary Lean Product Development, New York: Amacom, 2010.
[3] J. M. Quigley and S. G. Lauck, Cost Efficiency Unleashed: Exploring Advanced Strategies for Product and Process Improvement, Lexington, NC: Value Transformation LLC, 2024.
[4] K. Ishikawa, Introduction to Quality Control, 3A Corporation, 1997.
[5] K. Pries and J. M. Quigley, Total Quality Management for Project Management, Boca Raton: CRC Press, 2012.
[6] K. Pries and J. M. Quigley, Project Management of Complex and Embedded Systems, Ensuring Product Integrity and Program Quality, Boca Raton: CRC Press, 2008.
[7] G. Taguchi, S. Chowdhury and Y. Wu, Taguchi’s Quality Engineering Handbook, Livonia, MI: John Wiley & Sons, Inc., 2005.
[8] K. H. Pries and J. M. Quigley, Testing Complex and Embedded Systems, Boca Raton, FL: CRC Press, Taylor & Francis Group, 2011.
[9] A. Gulve and J. M. Quigley, “Modernizing Product Development Processes: Guide for Engineers,” Warrendale, PA, Society of Automotive Engineers Publishing, 2023.
[10] Bothe, Reducing Process Variation Using the DOT Star Problem Solving Strategy, Cedarburg, WI: Landmark Pub, 2002.
Elevate your project management skills and propel your career forward with an MPUG Membership. Gain access to 500+ hours of PMI-accredited training, live events, and a vibrant online community. Watch a free lesson and see how MPUG can teach you to Master Projects for Unlimited Growth. JOIN NOW