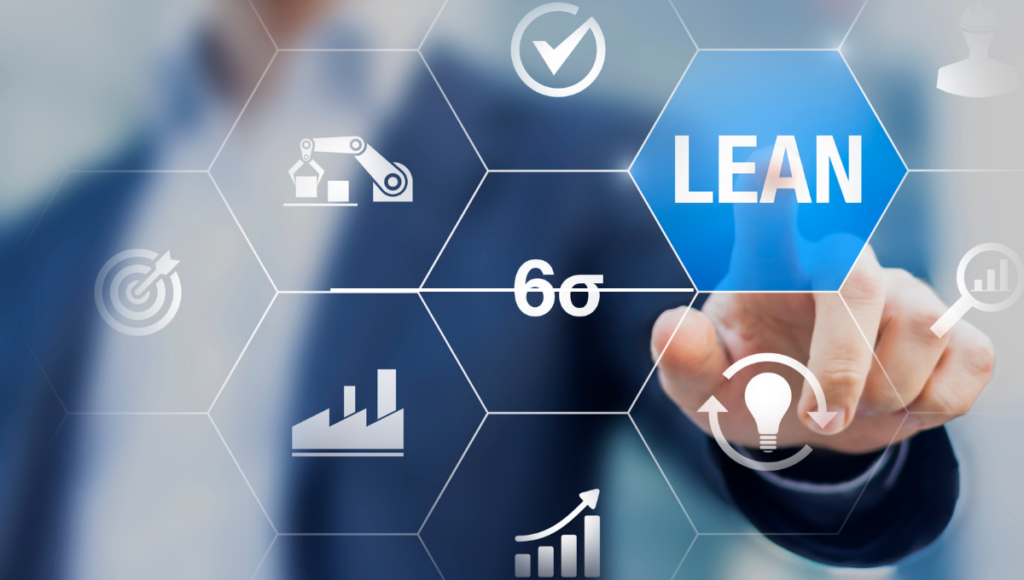
As a project manager, you’re always looking for ways to improve processes, eliminate inefficiencies, and deliver better results for your organization. Lean Six Sigma is a powerful project management methodology that can help you achieve these goals by providing a structured, data-driven approach to problem-solving and continuous improvement.
Understanding the DMAIC Process
At the heart of Lean Six Sigma is the DMAIC process, which stands for Define, Measure, Analyze, Improve, and Control. This five-step methodology guides you through the process of identifying, analyzing, and resolving complex problems within your organization.
- Define: Clearly define the project’s goals, scope, and customer requirements. Create a process map to visualize the current state and identify potential areas for improvement.
- Measure: Determine the key metrics and data needed to assess the current performance of the process. Establish a data collection plan, gather the necessary data, and calculate baseline performance.
- Analyze: Examine the collected data for trends, patterns, and outliers. Apply statistical tools and techniques to identify the root causes of problems and prioritize areas for improvement.
- Improve: Develop and implement solutions to address the identified root causes. Generate potential solutions, evaluate their feasibility, and select the best options for implementation. Monitor the impact and results of the improvements.
- Control: Establish processes and controls to ensure that the improvements are sustained over time. Document the improved process, establish monitoring and control mechanisms, train employees on the new process, and continuously evaluate and adjust as needed.

SIX SIGMA METHODOLOGY
When to Apply Lean Six Sigma
Lean Six Sigma is particularly well-suited for projects aimed at improving processes, eliminating waste, and increasing efficiency. While Lean Six Sigma is a powerful and widely applicable methodology, agile and waterfall are other popular project management methodologies. Consider applying this methodology when facing the following challenges:
- Improving Sales Conversions: If you’re struggling with low conversion rates in your sales process, Lean Six Sigma can help you identify and eliminate the root causes. By analyzing your sales funnel, pinpointing bottlenecks, and implementing targeted improvements, you can boost your conversion rates and drive better results.
- Eliminating Bottlenecks: If you’re experiencing significant delays or backlogs in your production or service delivery processes, Lean Six Sigma can help you identify and eliminate the bottlenecks. By mapping out the entire process flow and pinpointing the specific areas causing constraints, you can implement targeted improvements to streamline your operations.
- Reducing Defects and Enhancing Quality: If you’re facing quality issues, such as high defect rates or customer complaints, Lean Six Sigma can help you identify the root causes and implement preventive measures. By analyzing data and thoroughly understanding the production or service delivery process, you can identify opportunities for quality improvement and implement robust control mechanisms.
- Optimizing Resource Utilization: If you’re struggling with inefficient resource allocation or utilization, Lean Six Sigma can help you streamline workflows and optimize resource deployment. By analyzing process data and identifying waste, you can implement leaner processes and maximize resource utilization.
MPUG has provided Project Management Training for industry leaders for over 15 years. See how MPUG can help you achieve your professional goals and deliver successful projects. Visit MPUG.com today to access our comprehensive library of courses, webinars, and articles, and join our community of project management experts.
Key Considerations for Project Managers
When applying Lean Six Sigma to your projects, keep the following considerations in mind:
- Data-Driven Approach: Lean Six Sigma relies heavily on data and statistical analysis. Ensure that you have the necessary tools, skills, and resources to collect, analyze, and interpret data effectively.
- Stakeholder Engagement: Involve key stakeholders throughout the DMAIC process, from defining the problem to implementing and sustaining improvements. Their input, support, and buy-in are crucial for the success of your project.
- Continuous Improvement Mindset: Lean Six Sigma is not a one-time fix but a continuous improvement journey. Foster a culture of ongoing learning, experimentation, and adaptation within your team and organization.
- Training and Skill Development: Invest in training and skill development for yourself and your team members. Lean Six Sigma requires a solid understanding of statistical tools, problem-solving techniques, and change management principles.
By embracing Lean Six Sigma and applying the DMAIC process to your projects, you can drive significant improvements in efficiency, quality, and customer satisfaction. As a project manager, you play a crucial role in leading and facilitating this transformative journey within your organization.